Rigorous Quality Testing
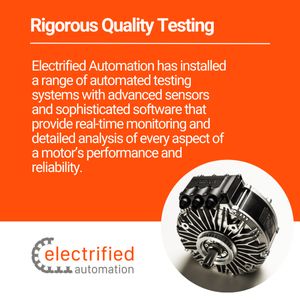
The high levels of automation we use throughout our manufacturing processes mean our customers can trust that Electrified Automation motors are produced to the highest standards and put through rigorous quality testing.
Every IPM motor that comes off our production line is tested for:
- Electrical safety: Stators and motors are tested for electrical resistance with up to 3000V (Hipot). A range of other electrical tests are also conducted with the automated stator test machine.
- Electromagnetic performance: Measuring the electrical and magnetic properties of the motor to ensure it meets our critical criteria, ensuring maximum efficiency and performance.
- Thermal Sensor: Checking the sensor itself thoroughly for correct operation and ensuring the temperature rise is correct.
- Position Sensor: Testing the sensor characteristics are in line with the specification eg voltages, current, angle, latency etc.
- Leak detection: All motors are tested to ensure the seal is correct and the motor will meet the IP rated design (such as the IP69K as standard).
- Noise and Vibration: Minimal noise and vibration for smooth operation.
- Integration and Compatibility: Parts are quality checked to ensure the tolerances are met and each process is capable.
- Coast down: All motors go through a powered test. Losses are measured to ensure correct operation and maximum efficiency can be achieved.
Electrified Automation has also installed a range of automated testing systems with advanced sensors and sophisticated software that provide real-time monitoring and detailed analysis of every aspect of a motor’s performance and reliability.
- Performance Testing
Efficiency Testing: The motor’s efficiency is measured under various loads to ensure it meets the specified performance criteria.
Power Density Verification: The motor’s power output is tested relative to its size and weight.
- Thermal Testing
Heat Run Test: The motor is operated at full load for extended periods to evaluate its thermal stability and cooling efficiency.
Temperature Rise Test: Measuring the increase in motor temperature under various loads and normal operating conditions ensures it meets all requirements and duty cycle demands.
- Durability and Reliability Testing
Lifecycle Testing: We simulate extended usage to identify potential points of failure and ensure the motor’s operational lifespan meets the requirements.
Shock and Vibration Testing: The motor’s resilience to mechanical shocks and vibrations is assessed, which can be common in industrial and automotive applications. We also combine these tests with thermal cycling to ensure harsh temperature changes are also tested.
- Control Precision Testing
Speed and Torque Accuracy: We evaluate the motor’s ability to maintain precise control over speed and torque, critical for applications requiring high precision.
Response Time Analysis: Measures how quickly the motor responds to control inputs.
- Noise and Vibration Testing
Acoustic Testing: Utilising sound measurement equipment confirms the motor operates within acceptable noise levels.
Vibration Analysis: Detecting and analysing vibrations ensures they are within acceptable limits and won’t cause premature wear.
- Integration and Compatibility Testing
System Integration Test: We verify the motor’s compatibility with different control systems and power sources.
Interface Testing: Ensuring that communication and power interfaces function correctly.
- Environmental and Regulatory Testing
Compliance Testing: Every motor meets is verified against all relevant industry standards and regulations, such as IEC and IEEE.
Environmental Testing: Assessing the motor’s performance in various environmental conditions, including extreme temperatures, EMC testing, salt spray and ingress protection (such as IP69K testing and certification).
- Material and Build Quality Testing
Material Analysis: We inspect the materials used in the motor for quality and durability.
Build Inspection: Conducting thorough inspections of the motor’s construction identifies any defects or weaknesses.
Quality comes as standard with an Electrified Automation motor, delivering performance, power and efficiency for a range of two-wheel and off-highway applications.